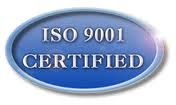
ISO 9000 is a series of international quality standards that have been developed by the International Organization for Standardization. More than 100 countries now recognize the 9000 series. The idea behind the standards is defects (or poor service) can be prevented through the planning and application of best practices at every stage of business—from design through manufacturing and then installation and servicing. These standards focus on identifying criteria by which any organization, regardless of whether it is manufacturing or service oriented, can ensure that product leaving its facility meets the requirements of its customers. These standards ask a company to first document and implement its systems for quality management, and then verify, by means of an audit conducted by an independent accredited third party, the compliance of those systems to the requirements of the standards.
Regardless of whether an organization is involved in a total manufacturing operation, including design, or only inspection and testing process, it can develop a quality management system based on one of the ISO 9000 requirements standards. By design, these standards can accommodate variation from company to company and between economic sectors. It is simply up to each individual business to interpret the appropriate requirements standards of its own processes.
The principal standards within the group are ISO 9001, 9002 and 9003. These are the requirements standards, and all the other standards within the series are related to these three. Of these three, ISO 9001 is the most comprehensive. Divided into 20 specific elements, it provides a foundation for basic quality management and continuous improvement practices. Each of its 20 elements covers a particular area of an organization’s business processes:
1. Management Responsibility
2. Quality Planning
3. Contract Review
4. Design Control
5. Document & Data Control
6. Purchasing
7. Control of Customer-Supplied Product
8. Identification & Traceability
9. Process Control
10. Inspection & Testing
11. Control of Inspection, Measuring & Test Equipment
12. Inspection and Test Status
13. Control of Nonconforming Product
14. Corrective & Preventive Action
15. Storage, Handling, Packaging Preservation & Delivery
16. Control of Quality Records
17. Internal Quality Audit
18. Training
19. Servicing
20. Statistical Technique
ISO 9002 and ISO 9003 are derivatives of the 9001 requirements standard. But why is it important to become ISO 9000 certified? For one reason, it is essential from a purely competitive standpoint. Simply stated, ISO 9000 compliance is “good business practice”. Adopting ISO 9000 should produce the following benefits:
• Improved efficiency of operations
• Optimized company structure & operational integrity
• Improved utilization of time and materials
• Clearly defined responsibilities and authorities
• Improved accountability of individuals, departments, and systems
• Improved communication and quality of information
• Improved records in case of litigation against the company
• Formalized systems with consistent quality, punctual delivery, and a
framework for future quality improvement
• Documented systems with useful reference and training tools
• Fewer rejects; therefore, less repeated work and warranty costs
• Rectified errors at an earlier stage; therefore, less scrap
• Improved relationships with customers and suppliers
• Ability to tender for ISO 9000 contracts at home and abroad
The ability of implementing ISO 9000 is directly proportional to management commitment. Executive management must realize that the quality element plays a key role in the success of the business. The quality system must be “lived day-to-day”. Its success or failure does not rest on the shoulders of the quality manager alone. If a business is not profitable, does management fire the finance manager? Of course not! A successful company is operated through teamwork.
It is interesting to note that according to the latest ISO Survey of Certifications -- 2007 reveals certification activity around one or more of ISO’s management system standards in 175 countries, up from 170 in 2006 – “a clear demonstration”, according to the survey, “that they have become essential tools of the world economy”. ISO Secretary-General Alan Bryden comments: “The survey illustrates in a very concrete manner the extent to which ISO management system standards are meeting the organization’s strategic objective of ‘global relevance’ – in other words, adding value for the organizations that use them all over the world.” (ISO News 2008.)
-OM-
Rafael Pablo M. Fernando is currently the Officer-in-Charge of the Total Quality Management group of the Subic Bay Metropolitan Authority (SBMA). He is also connected with Integral Transformation Group, Inc., a transformative management group giving organizations and its people alternative forms of managing and living life to the fullest. Formed 1992, ITG-TheGroup extends management services, education & training, and advocacy activities in the areas of: quality management-ISO implementation, organic agriculture, cooperatives, sustainable development, Vedic culture, good governance, strategic planning, institutional development, among others. (February 25, 2010).
The behavior we observe in ourselves or in the people around us at any moment is only the external expression of what is going on inside us. Thus, to change behavior effectively, quality improvement (which is educational in nature), must concentrate not on external things like information, gadgets, and methods, but rather on altering the belief systems of the people who make the decisions and do the work.
ReplyDelete